Boost Your Requirements with Specialist Welding Inspection Milwaukee Solutions
Boost Your Requirements with Specialist Welding Inspection Milwaukee Solutions
Blog Article
Exactly How Welding Inspection Contributes to Longevity and Reliability in Fabrication Tasks
Welding inspection offers as a fundamental aspect in making sure the durability and reliability of fabrication tasks. By methodically determining potential problems during various phases of production, welding examinations not just stop costly failings yet additionally cultivate a society of quality control within the group. Using innovative methods, such as non-destructive testing, facilitates thorough examinations while protecting product stability. As projects proceed, the effect of these inspections comes to be progressively evident, elevating important questions about their lasting benefits and effects for overall task success. What particular techniques can be executed to take full advantage of these benefits?

Importance of Welding Inspection
Guaranteeing quality with welding examination is a crucial element of any type of fabrication job. It functions as a guard to verify that welding processes meet recognized requirements and specs, consequently boosting the total honesty of the framework or element being fabricated. Welding evaluation is not simply a procedural step; it is a vital method that assists determine prospective issues early, guaranteeing that they are dealt with before they escalate right into significant troubles.
The value of welding inspection can be underscored by its function in keeping safety and security and resilience. Welded joints are frequently subjected to severe problems, and any defects can compromise the efficiency and durability of the end product. By carrying out extensive inspection methods, companies can guarantee compliance with sector policies, thereby minimizing threats related to structural failings.
Furthermore, reliable welding examination promotes confidence amongst stakeholders, including customers and regulative bodies, that the job satisfies the finest quality criteria. This not just enhances the credibility of the fabricator however likewise adds to lasting expense savings by preventing rework and potential obligations. Inevitably, welding assessment is important to the success and dependability of manufacture tasks, enhancing the value of quality control in engineering methods.
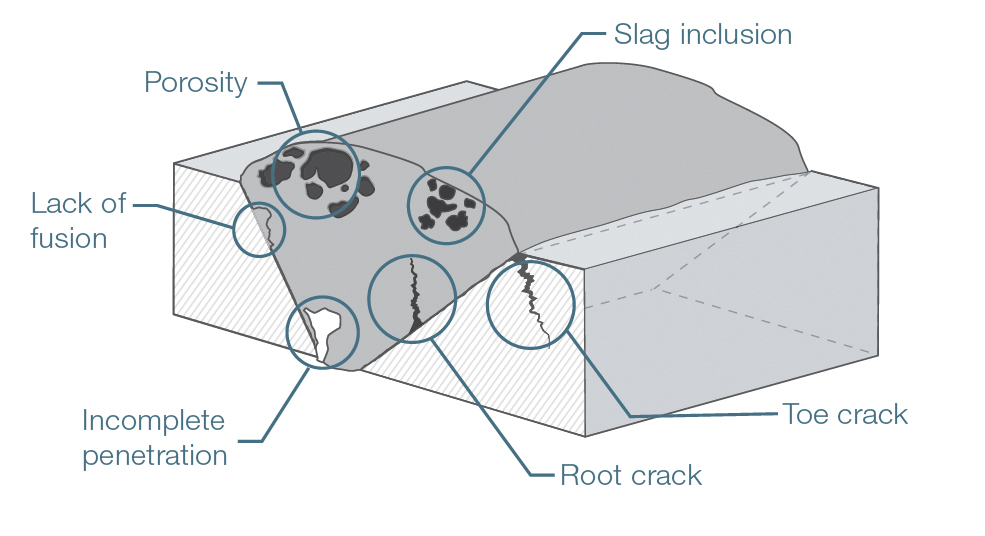
Common Welding Defects
Welding flaws can dramatically undermine the architectural stability of made elements, making their recognition and rectification critical. Common welding issues can be generally categorized into 3 kinds: geometric, metallurgical, and service-related.
Geometric issues consist of concerns such as undercutting, where the base metal is deteriorated beside the weld, and too much convexity, which can lead to stress and anxiety focus points. These problems can jeopardize the strength and toughness of the weld joint.
Metallurgical problems arise from improper welding treatments or products, leading to issues such as porosity, where gas pockets form within the weld, and absence of fusion, which happens when the weld metal falls short to bond properly with the base steel. These issues can substantially deteriorate the weld's effectiveness.
Service-related flaws may not end up being evident until after the part is in usage. Examples consist of splitting because of thermal stress and anxiety or exhaustion, which can cause catastrophic failings otherwise attended to.
Comprehending these common issues equips producers to implement efficient evaluation strategies that boost the dependability and long life of their tasks, ultimately ensuring security and performance criteria are met.
Examination Strategies and Approaches
A thorough technique to evaluation methods and methods is necessary for reducing and identifying welding defects in fabrication jobs. Various techniques are used to ensure the honesty of welds, consisting of aesthetic evaluation, ultrasonic screening (UT), radiographic testing (RT), magnetic bit testing (MT), and dye penetrant screening (PT) Each technique has its staminas and details applications.
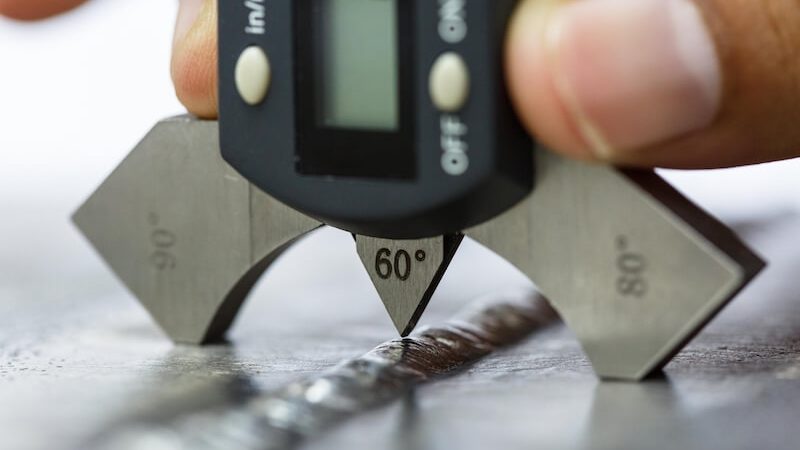
Magnetic particle screening is beneficial for detecting surface area and near-surface defects in ferromagnetic products. By using an electromagnetic field and using ferrous bits, inspectors can determine suspensions effectively. Color penetrant screening highlights surface-breaking defects with the application of a color that seeps right into splits, making them visible under ultraviolet light.
Utilizing a mix of these methods makes sure a strenuous assessment, improving the integrity of welded structures.

Influence on Job Longevity
Effective inspection techniques significantly influence the long life of manufacture tasks. By determining potential problems and disparities in welding procedures, evaluations guarantee that frameworks are developed to endure operational stresses with time. When welds are extensively taken a look at, the possibility of unseen concerns, which might result in structural failings, is lessened.
Regular Homepage inspections promote adherence to market standards and laws, which are essential for ensuring the durability of bonded joints. Such compliance not just improves the integrity of the task however likewise comforts stakeholders relating to the quality of the job. Moreover, timely discovery of flaws enables restorative actions to be taken early, protecting against pricey fixings or total overhauls down the line.
Additionally, efficient inspection methods cultivate a culture of top quality guarantee within manufacture teams. When employees realize that their work will certainly be rigorously assessed, they are extra likely to comply with finest practices and preserve Visit Your URL high criteria throughout the production procedure. Inevitably, this dedication to high quality not just extends the life expectancy of the job but likewise reduces upkeep prices, thus improving the general financial viability of construction undertakings.
Enhancing Reliability in Construction
Dependability in fabrication is dramatically boosted via rigorous inspection procedures that attend to possible weaknesses in welding methods. Efficient welding evaluation not only determines defects early however additionally gives crucial comments to welders, making certain adherence to established requirements and specs. By using non-destructive screening techniques, such as radiographic or ultrasonic inspections, makers can determine the honesty of welds without compromising the product.
Furthermore, routine inspections promote a culture of quality and responsibility amongst manufacture teams. They are a lot more likely to adhere to best methods and methods when welders recognize that their job is subject to stringent evaluations. This aggressive approach reduces the threat of costly failures during the operational phase of a project.
In addition, thorough documentation of assessment results develops an important database of info that can be used for future tasks. Trends in flaws can be assessed to boost welding strategies and training programs (Welding Inspection Milwaukee). Inevitably, improving integrity in construction through extensive assessment refines not just enhances the lifespan of the made components yet additionally enhances stakeholder confidence in the project's overall top quality and toughness. Investing in robust welding assessment methods is necessary for attaining long-lasting integrity in any type of manufacture venture.
Verdict
In recap, welding assessment acts as a crucial part in ensuring the durability and reliability of manufacture tasks. By identifying defects early and employing non-destructive testing techniques, evaluations foster a culture of quality control that complies with market standards. The systematic documentation of results not only promotes trend analysis yet also improves responsibility and architectural stability. Inevitably, efficient welding examination methods enhance stakeholder confidence and significantly add to the economic feasibility of manufacture ventures.
Welding evaluation serves as a fundamental element in read more guaranteeing the longevity and dependability of manufacture tasks.Making certain high quality with welding examination is a critical part of any type of fabrication job. Eventually, welding evaluation is essential to the success and integrity of construction jobs, strengthening the value of high quality guarantee in engineering techniques.
A comprehensive method to inspection strategies and methods is important for reducing and identifying welding defects in fabrication jobs.In summary, welding evaluation offers as an important part in making certain the longevity and dependability of manufacture jobs.
Report this page